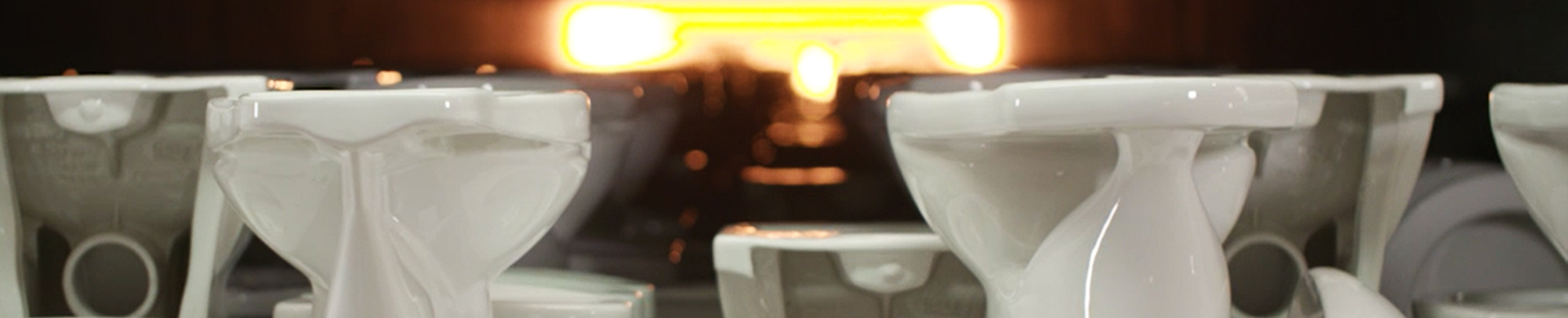
TABLEWARE
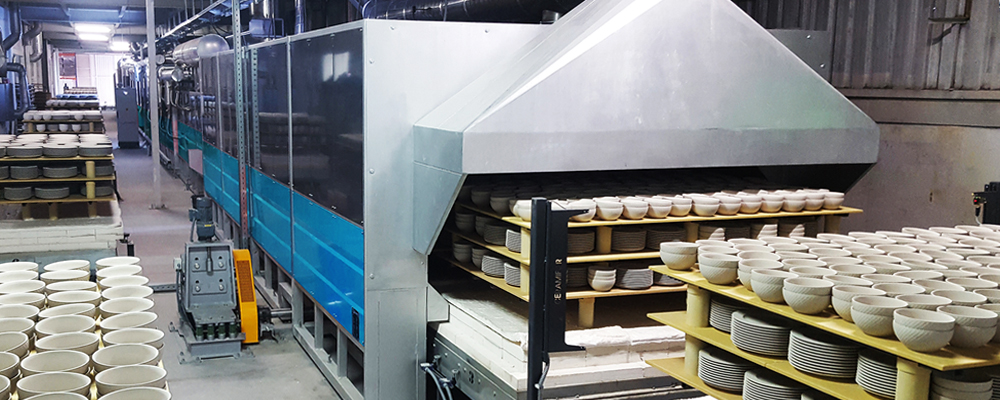
Customized solutions, studied according to the needs and requirements of each customer, depending on the type of parts and size of the load, the exhaustion process, the firing curves and atmospheres
Efficient control of temperature, pressure and atmosphere, in order to meet the highest quality standards, with automatic air/gas mixing control systems in gas ovens, allowing a more efficient control of the atmosphere, with the option of installing equipment for the analysis and continuous monitoring of O2 and CO.
KILNS UP TO 1 420°C
STANDARD MODELS FOR TABLEWARE, DECORATION AND OTHER
SANITARY
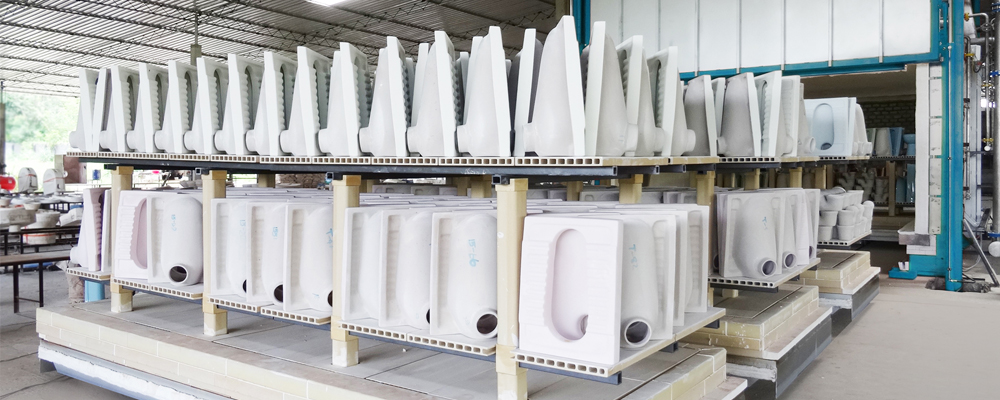
Customized designs, conceived and tested according to the type and size of the items, the load, and the type of refractory equipment. Exhaustion systems considering the best performance conditions of the kiln.
Efficient control of temperature, pressure and atmosphere, to meet the highest quality standards, with automatic stirring control systems in gas kilns allowing more efficient control of the atmosphere, with the option of installing equipment for the analysis and continuous monitoring of O2 and CO. Secondary air for efficient cooling of the load and faster firing cycles.
Automatic doors with guillotine and frontal or lateral movement, adapted to each project.
KILNS UP TO 1300°C
STANDARD MODELS
TECHNICAL CERAMICS & REFRACTORIES
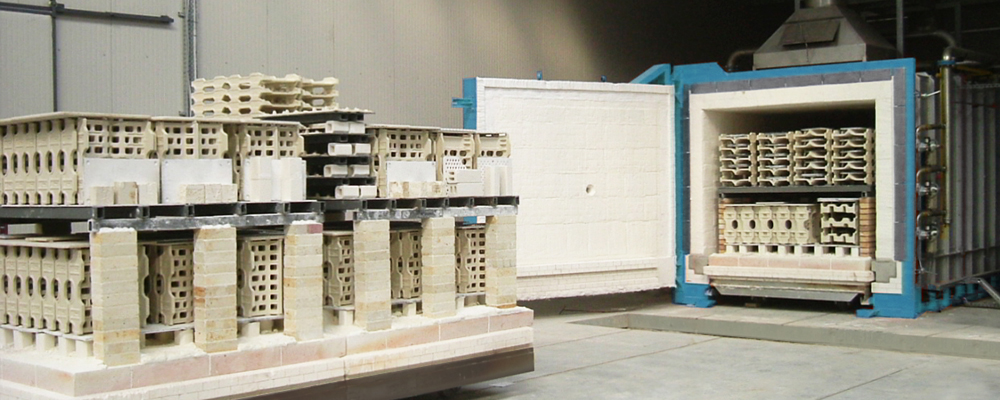
Designed for products with high temperature and atmosphere control requirements, usually slow cycles, where the precision of control has a high impact on the quality of the final result.
Hot air recovery systems that can increase efficiency and generate significant energy savings – for gas furnaces. The air heating process includes a group of equipments and components that allow – starting from exhaustion gases – to heat the combustion air (clean) to a maximum inlet temperature at the burners at 400°C.
Possibility to supply the post-combustion system, in case of need of gas treatment.
KILNS UP TO 1700°C
FIXED SOLE, WAGONETS OR TOP HAT
ABRASIVES
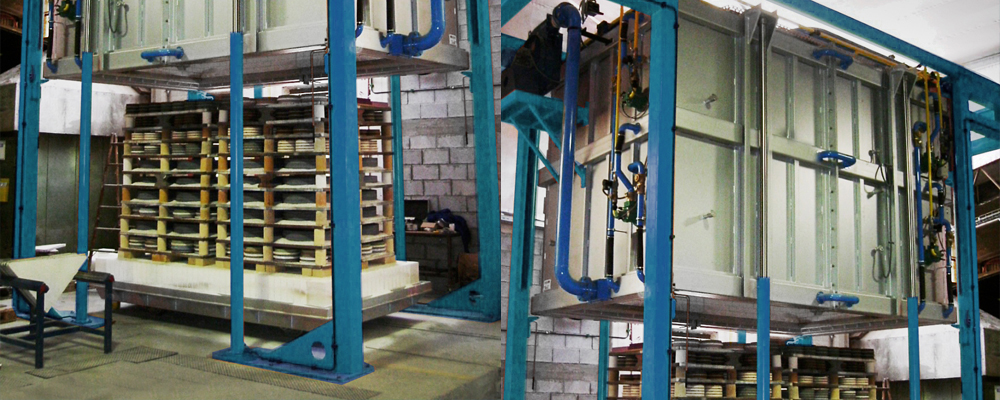
Products with high temperature and atmosphere control requirements, requiring longer and controlled firing curves, specifically for the release of various binder materials.
Hot air recovery systems that can increase efficiency and generate significant fuel savings – for gas furnaces. The air heating process includes a group of equipments and components that allow – starting from the exhaustion gases – to heat the combustion air (clean) to a maximum inlet temperature at the burners at 400°C.
The kilns, mainly gas fired for this type of cooking, are usually equipped with an afterburner chamber with a working temperature of up to 800°C. This equipment allows the combustion of several compounds in the exhaust gases in compliance with environmental standards.
KILNS UP TO 1700°C
FIXED SOLE, WAGONETS OR TOP HAT
STRUCTURAL
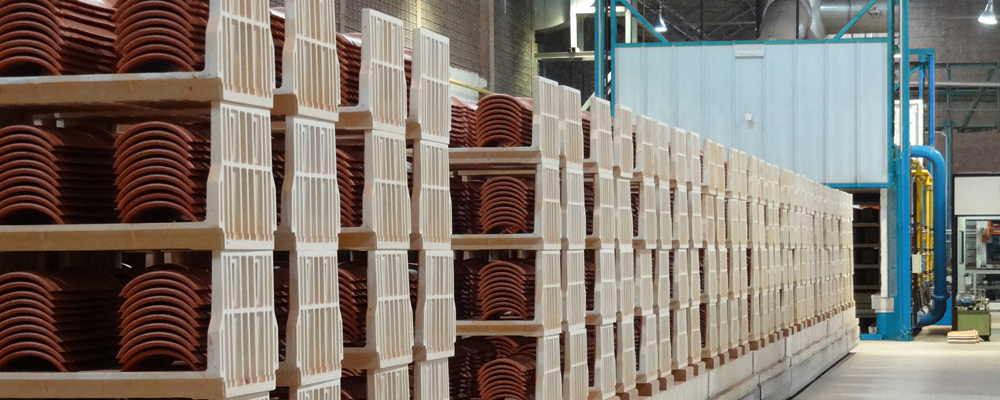
Traditionally of upper exhaustion; can be of inverted exhaustion if the load is not made directly on the wagon, for example on gazettes for automatic loading and unloading.
Integration with automatic systems for loading and unloading.
KILNS UP TO 1200°C
HEAVY LOADS
TERRA COTTA
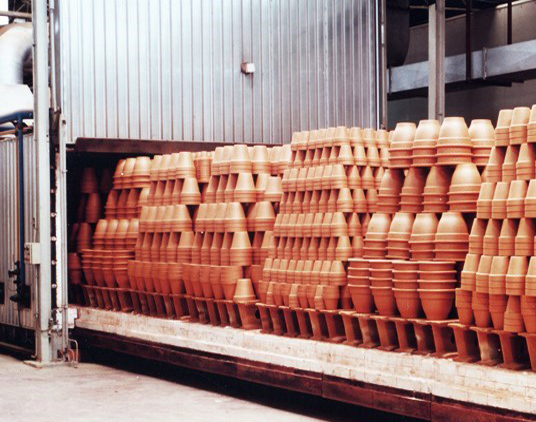
Customized designs, studied according to the type and size of the items, the load, the exhaustion process, firing curves and atmospheres.
Efficient control of temperature, pressure and atmosphere, in order to meet the highest quality standards, with automatic mixing control systems in gas ovens allowing a more efficient control of the atmosphere.
KILNS UP TO 1100°C
HEAVY LOADS
NEED MORE TECHNICAL INFORMATION?
Would you like to receive more technical information by e-mail?
Please tell us more about you and your project.